caros amigos mais uma vez estamos juntos para falar sobre os freios confira a primeira parte do especial aqui porem hoje iremos muito alem da segurança um conjunto de freios bem projetado permitira que um bom piloto freie mais tarde e mais que isso mantenha a consistencia das frenagens durante a prova sem que haja perda na dirigibilidade hoje nos vamos entender como dimensionar o sistema quais as forças atuantes e como realizar as melhores escolhas para os nossos projetos requisitos de projeto [caption id= attachment_233022 align= aligncenter width= 960 ] navigation[/caption] para que possamos ir a um local desconhecido precisamos de referencias seja um endereço um par de coordenadas geograficas ou mesmo um roteiro a seguir a partir dai traçamos o nosso caminho no mapa o mesmo acontece aqui precisamos de informaçoes basicas sobre o veiculo para iniciarmos os calculos massa do veiculo; posiçao horizontal do centro de gravidade; altura do centro de gravidade leia aqui ; dimensoes de pneus e rodas; velocidade maxima pretendida; uso previsto padroes ou metas a serem alcançados estes dados nos darao referenciais para o calculo da transferencia de peso no momento da frenagem e a consequente carga aplicada sobre cada eixo entao antes de começar qualquer calculo do sistema de freios nos precisamos saber qual o coeficiente de adesao dos pneus antes deles começarem a derrapar para estudos de engenharia aplicada legislaçoes e desenvolvimento de pneus ha diversas equaçoes que trazem a fidelidade necessaria mas o nosso caso de estudo um texto tecnico introdutorio nao pede esse nivel de precisao neste caso utilizaremos uma tabela de aproximaçao para o coeficiente de adesao dinamico quando o pneu nao esta sendo arrastado com essas informaçoes vamos a um exemplo ze do breque resolveu montar um ka 2005 para se divertir como ele sempre faz a tarefa de casa o ze fez todas as mediçoes da lasanha e anotou a seguinte ficha massa total 893 kg entre eixos 2448 mm altura do centro de gravidade 663 mm posiçao horizontal do centro de gravidade 832 3 mm / 1615 7 mm dimensoes das rodas 15 x 6 5 dados dos pneus 205 / 565 r15 pista transferencia de peso longitudinal quando nao ha força de aceleraçao positiva ou negativa atuando sobre o veiculo a transferencia de peso nao existe entao a carga sobre cada eixo vai depender da distribuiçao de massa vamos calcular a carga de cada eixo para termos a base para as etapas seguintes o limite de desaceleraçao de qualquer veiculo fica entre o limite de adesao dos pneus e o limite de transferencia de peso aquele que apresentar o menor valor sera o limiar de escorregamento dos pneus durante uma frenagem em linha reta a quantidade de peso transferida do eixo traseiro para o dianteiro depende desaceleraçao provocada a maxima transferencia acontece quando alcançamos o limite de desaceleraçao com a maxima transferencia de peso nos podemos encontrar a carga aplicada a cada eixo e os respectivos limites de aderencia com o uso de pneus slick o limite de desaceleraçao passou a ser o limite de transferencia de peso do veiculo nessa condiçao todo o peso se concentraria no eixo dianteiro tornando a traseira instavel entao e necessario redistribuir a força entre os eixos de modo a manter a maxima capacidade de frenagem mas com uma menor transferencia de peso para recalcular as cargas nos utilizamos a seguinte equaçao de equilibrio agora podemos definir as novas cargas sobre os eixos dianteiro e traseiro a partir dos novos limites de aderencia ergonomia da frenagem e pedais de competiçao https //www youtube com/watch v=lgk1p3 3kgy por questoes de segurança estudos definiram que num carro de rua a força maxima que deve ser exercida pelo motorista sobre o pedal do freio deve estar entre 445 e 823 newtons mas quando tratamos de carros de competiçao valores entre 850 e 1400 newtons sao esperados principalmente levando em conta que para estas maquinas normalmente nao ha servo assistencia devido a divisao dos circuitos de freios falaremos sobre este assunto mais adiante alem do esforço maximo realizavel a distancia de deslocamento do pedal deve ser controlada para que as reaçoes sejam curtas o curso maximo percorrido pelo embolo do cilindro mestre e seu eixo consequentemente deve ser de 30 mm enquanto o curso admissivel para que o sistema alcance a pressao maxima fica entre 10 e 12 mm entao a depender do fator de multiplicaçao do pedal o curso pode chegar a quase 200 mm este fator de multiplicaçao se deve pela alavanca formada pelo pedal que tem o intuito de amplificar a força exercida pelo motorista por exemplo se o pedal tem razao de 4 1 e o motorista aplica uma força de 500 n a força aplicada ao eixo do cilindro mestre sera de 2000 n sistemas de frenagem que possuem servo assistencia normalmente apresentam relaçoes de 4 1 e 5 1 e aqueles que nao tem esse artificio se utilizam de relaçao entre 5 1 e 7 1 quando falamos de pedais voltados para competiçao ha algumas diferenças construtivas uma das mais importantes e a capacidade de ajuste da distribuiçao de frenagem entre os eixos atraves de um dispositivo chamado barra de balanço de freio a barra e ligada a dois cilindros mestre cada um deles comanda um eixo quando a barra e girada ela se desloca no fulcro aumentando seu comprimento relativo a um dos cilindros entao pelo principio de arquimedes aquele da alavanca a distribuiçao da força aplicada muda entao como num pe de cabra a parte mais longa da alavanca aplica uma quantidade de força menor que a parte mais curta entao podemos definir a força aplicada a cada cilindro atraves das equaçoes dimensionamento dos discos e pinças e ergonomia com os valores das forças de frenagem definidos nos podemos iniciar o dimensionamento dos discos e pinças mas antes de rabiscar qualquer equaçao busque por catalogos dos fabricantes tenha em maos as dimensoes dos discos originais para referencia verifique a necessidade de modificaçao dos suportes das piças voce provavelmente vai precisar fazer isso e claro se voce e iniciante no assunto procure um profissional gabaritado abaixo temos uma tabela para referencia dos diametros maximos de discos para cada diametro de roda por razoes obvias eu coloquei apenas as dimensoes mais comuns no nosso pais os discos de freio sao solidarios ao movimento dos eixos entao quando a força de frenagem e aplicada contra os discos e gerado um torque vetor de força aplicada em rotaçao entao este torque tem relaçao direta com o raio do disco de freio ou seja quanto maior o disco maior o torque aplicado ao eixo de rotaçao mas ha limites nesse sentido alem das questoes de dimensionamento a inercia de uma massa rotativa muito grande ira prejudicar as frenagens e aceleraçoes por isso procure sempre o equilibrio nas suas escolhas o diametro do pneu tem relaçao inversa a força de frenagem pois a força de adesao gerada pela area de contato do pneu com a superficie esta distante do ponto de aplicaçao da força de frenagem entao quanto maior o raio do pneu menor sera a carga aplicada sobre o eixo outro fator de influencia e o coeficiente de atrito das pastilhas ja falamos sobre caracteristicas das pastilhas aqui sendo os raios e o coeficiente de atrito fatores estaticos o unico fator que fara a carga sobre os eixos variar e a força aplicada as pastinhas convertendo as unidades temos mais de tres toneladas de força aplicada a primeira vista esse numero pode parecer bem estranho e ate improvavel mas vamos fazer alguns calculos para vermos qual a quantidade de força que deve ser aplicada ao pedal primeiro determinamos os fatores fixos da equaçao escolhemos um disco de 278 mm de diametro 45 mm de pista e raio efetivo de 118 4 mm para as pastilhas a escolha ficou com um composto de coeficiente de atrito 0 63 e temperatura de operaçao 380°c e 20 mm de espessura maxima de desgaste as pinças possuem quatro pistoes de 26 e 30 mm e area total de 2475 mm² 0 002475 m² com estes dados em maos vamos fazer uma serie de calculos para descobrir quanta força deve ser aplicada ao pedal para alcançarmos a maxima desaceleraçao se as pastilhas exercem uma força de 33707 4 newtons e a area para a aplicaçao desta e de 0 002475 m² a força exercida pelos pistoes e resultado da pressao do sistema hidraulico entao a pressao do circuito dianteiro e gerada pelo cilindro mestre que e acionado pelo usuario atraves do pedal de freio por questoes de segurança vamos determinar que a força maxima realizada pelo motorista sera de 870 newtons o pedal tem fator de multiplicaçao de 6 1 entao a força atuante sobre o cilindro e de 5220 n utilizando a equaçao da pressao temos com a area em maos podemos calcular o volume deslocado pelo cilindro e comparar com o volume necessario para que o sistema mantenha sua capacidade maxima ate o limite de desgaste das pastilhas como vimos acima o curso do embolo do cilindro mestre deve ser limitado a 30 mm 0 03 m como o volume de um cilindro e resultado da area da sua base multiplicada pela altura entao com o valor de referencia nos devemos buscar no catalogo as medidas mais proximas lembrando que esta preferencialmente nao deve ser menor que o valor calculado pois isto implica num aumento da força a ser aplicada pelo motorista encontramos um cilindro com 20 64 mm de diametro o volume de fluido hidraulico necessario para deslocar os pistoes ate o limite de desgaste das pastilhas e fornecido pelo reservatorio entao precisamos calcular o volume necessario para que as pastilhas cheguem ao seu limite e nao haja uma pane seca no sistema devemos levar em conta a area total das duas pinças ou seja quatro vezes a area que usamos como referencia da mesma forma que antes nos devemos buscar no catalogo um reservatorio com capacidade maior que a calculada preferencialmente com 20% ou mais de volume para evitar a cavitaçao durante as frenagens mais fortes essa mesma sequencia deve ser usada para dimensionarmos o sistema de freios traseiro mas devemos levar em conta que a força aplicada ao pedal e a mesma porem a força de frenagem a ser aplicada deve ser a anteriormente calculada para este eixo numero de pistoes e localizaçao das pinças quando nao conhecemos bem o assunto e normal imaginar que uma pinça com uma quantidade maior de pistoes pode gerar uma força de frenagem maior bem como vimos acima o fator de maior influencia para a frenagem e a força exercida sobre o pedal a funçao das pinças de multiplos pistoes e permitir que a força seja distribuida de forma mais equilibrada durante a frenagem existe uma tendencia natural de que as pastilhas se inclinem em direçao ao sentido de rotaçao do disco se a força aplicada as pastilhas nao compensar esta tendencia nos teremos um desgaste angular e prematuro do material de atrito alem de uma distribuiçao heterogenea da temperatura pelo disco e pastilha para evitar estas situaçoes os fabricantes buscam diversas soluçoes de projeto uma soluçao comum e a utilizaçao de pistoes deslocados do centro da pinça isso gera uma assimetria na aplicaçao da força o que se contrapoe a tendencia de inclinaçao das pastilhas sistemas teves hammerhead realizam a mesma funçao utilizando prolongamentos dos suportes como limitadores de movimento porem quando falamos de alta performance estas soluçoes se mostraram pouco eficazes pois acabavam por reduzir a força efetivamente aplicada no limiar de frenagem foi entao que os projetistas decidiram pela aplicaçao nao uniforme da força atraves de pistoes de diferentes diametros a ideia e simples se a pressao aplicada aos pistoes e igual a forma exercida por eles sera diretamente proporcional a suas respectivas areas por esse motivo temos pinças de multiplos pistoes com tamanhos diferentes os pistoes tem diametro crescente no sentido de rotaçao do disco por isso pinças com multiplos pistoes possuem posiçao a ser instalada outra questao que determina a posiçao de instalaçao das pinças e o ponto de sangria que deve sempre estar na posiçao mais alta pois assim e garantido que nao haverao bolhas dentro das camaras falando em posiçao voces ja repararam que as pinças variam de posiçao de acordo com o tipo de veiculo que observamos na foto acima a diferença de posiçao e clara isso se deve a necessidade de um melhor posicionamento da massa nao suspensa e do centro de gravidade com o tempo os projetistas perceberam que manter essa massa mais proxima do centro e o mais baixa possivel ajuda sensivelmente na dirigibilidade e reaçoes do veiculo em casos extremos como na f1 as pinças sao posicionadas o mais baixo possivel entao se voce estiver montando um projeto e a geometria da sua posiçao permitir mantenha as pinças para dentro do eixo e o mais baixo que voce puder monitoramento de temperatura ok sabemos que as pastilhas e os discos possuem uma temperatura ideal de operaçao mas como saber se voce esta realmente operando na faixa correta sera que passou do ponto ou nem chegou la imagine uma situaçao dessas numa equipe de corrida onde todos os dados possiveis fazem diferença como a necessidade e a mae da maioria das invençoes os engenheiros foram buscar nas industrias a soluçao entao os discos passaram a receber faixas de tinta termo sensivel a cor tinta muda em uma temperatura especifica e mesmo que ela se resfrie depois nao volta a cor anterior com isso basta aplicar tintas com tres temperaturas sets diferentes uma abaixo do ideal uma muito proxima e outra acima para monitorar se o piloto esta levando os freios ao ponto otimo passando do limite ou nao chega nem perto mas como no mundo dos esportes a motor ninguem se sente satisfeito com o que tem os engenheiros queriam mais precisao nas informaçoes com isso foram criados adesivos termo sensiveis com uma barra de indicaçao assim uma informaçao mais detalhada pode ser lida ao final de cada sessao ao final da sessao ai estava o problema um engenheiro que se preze quer a informaçao na hora ao vivo em cores e alta resoluçao nao estamos falando de pixels por polegada mas sim de amostras de sinal por segundo assim ele pode chamar a atençao do piloto pelo radio ouvir uma resposta no melhor estilo do raikkonen entao as equipes passaram a utilizar sensores de infravermelho para monitorar os freios em tempo real sera que cabe depois de todo esse trabalho de dimensionar escolher entre as inumeras opçoes dos catalogos guardar seu rico dinheirinho e torcer pro pessoal do buraco negro de curitiba liberar sua encomenda voce vai instalar as piças na sua lasanha e descobre que as rodas que voce comprou antecipadamente nao se dao bem com o sistema que voce escolheu para que isso nao aconteça com voce jovem o flatout traz um guia ilustrado que vai te safar dessa onça passo 1 se voce ja tem as rodas faças as mediçoes do espaço disponivel na parte traseira da roda passo 2 com as dimensoes na cachola verifique as medidas que constam no manual e desenhe um esboço alguns fabricantes disponibilizam estes rascunhos nos seus sites passo 3 coloque o esboço sobre o assentamento do cubo e verifique o espaço livre na roda veja se ha pelo menos 3 mm de distancia no ponto mais proximo se deu tudo certo monte seu conjunto e seja feliz mas se houver interferencia voce pode optar por outro conjunto um chapeu mais concavo rodas com offset diferente ou mesmo espaçadores carbono ceramica e os novos limiares para os freios com certeza voce ja viu videos fotos e textos sobre os discos de carbono ceramica eles estao nos carros que habitam nossos sonhos e nas categorias de ponta dos esportes a motor esse material começou a ser usado na aviaçao em 1969 com o concorde no mundo das quatro rodas esses freios apareceram dez anos depois com a brabham na f1 e finalmente em 2001 a porsche foi a primeira fabricante a aplica los num carro de produçao as vantagens desse tipo de sistema ficam por conta do seu baixo peso ate 70% inferior aos discos de aço grande resistencia ao desgaste e principalmente a potencia de frenagem que pode ser gerada e sua capacidade de gerenciamento de calor as desvantagens ficam por conta do custo e do feedback menor em relaçao aos discos de aço na f1 a evoluçao trouxe a evoluçao para discos de puro carbono operando entre 350 °c e 1000 °c com peso de apenas 1 5 kg o grande desafio neste caso e a refrigeraçao dos discos os engenheiros descobriram que pequenos canais permitem uma melhor refrigeraçao para esse tipo de material sao cercar de 1200 canais que geram um grande fluxo de ar atraves do disco mantendo um bom controle de temperatura por aqui nos encerramos o papo de hoje espero ter ajudado a esclarecer algumas duvidas e criado outras no nosso proximo papo vamos tratar das unicas coisas que mantem o contato com o solo em qualquer carro os pneus lembram daquele famoso logo da pirelli potencia nao e nada sem controle pois e vamos fazer um passeio atraves dessa filosofia ate la
SEJA UM MEMBRO DA
FAMÍLIA FLATOUT!
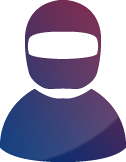
Ao ser um assinante, você ganha acesso irrestrito a um conteúdo verdadeiro e aprofundado. Nada de jornalismo genérico e sensacionalista. Vale a pena? Clique aqui e confira os testemunhos dos assinantes, amostras livres e os benefícios extras que você poderá desfrutar ao ser um FlatOuter!
PARA LER MAIS, CADASTRE-SE OU ASSINE O FLATOUT E TENHA ACESSO LIVRE A TODO CONTEÚDO DO SITE!
JÁ POSSUI CADASTRO OU É ASSINANTE DO FLATOUT?
Este é um conteúdo restrito: pode ser uma matéria só para assinantes, pode ser porque você já atingiu o limite de matérias gratuitas neste mês.